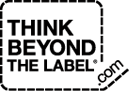
Job Information
Novolex Maintenance Manager / Plant Engineer in Yakima, Washington
Why Choose Us? Novolex is a leader in packaging innovation, choice and sustainability. We manufacture products in paper, plastic and sustainable materials for the food, retail, health and industrial markets. $110,000 to $150,000 yearly base salary plus bonus opportunity. Wellness rewards to fund your HRA or HSA Full Medical Benefit options starting the following month after hire. Onsite Medical Clinic Paid holidays, time off, parental and other leaves Financial protection benefits such as life, AD&D and disability insurance, and 401(k) Plan with employer matching contributions Education Support (for example, tuition reimbursement, Chairman's Scholarship, 529 College Savings Plan) Broad Based Employee Award Program-value sharing plan for all employees with one year of service Employee Assistance Program and much more! *The range provided is based on cost of living/geography and what we believe is reasonable in the market at the time of posting. This role may be eligible for annual bonus and annual merit increase, as well as long term compensation. Some roles may also be eligible for overtime pay, in accordance with federal and state requirements. Actual base salary pay will be based on a number of factors, including skills, competencies, experience, and other job-related factors. Our Sustainability Commitment The Novolex sustainability vision is built upon three pillars: our products, our operations and our people. Each is critically important to our growth and future as a business. These pillars form the foundation of our company-wide commitment to sustainability, helping us achieve our ambitious goals through our wide-ranging initiatives. How You'll Perform the Role This position will provide proactive leadership, strategic direction, and technical support to the operations of the facility in the areas of preventive/predictive maintenance, process engineering, technology modernization, automation, process improvement, and cost improvement. Advance initiatives which promote and sustain the safety, health, and welfare of all personnel. Provide leadership and direction to the maintenance team. Inspire high performance through effective goal setting and performance measurement. Implement and institutionalize the Business Unit's standardized preventive and predictive maintenance system (utilizing TPM, Lean, Six Sigma doctrine). Design minimum effort shop floor / warehouse layouts and flow paths. Design, implement and institutionalize "best practice" quick change procedures, processes and equipment modifications (SMED). Design process and equipment safety modifications (added layers of protection). Teach, coach, develop, and lead personnel. Perpetuate continuous reduction in waste, downtime, setup/make ready, and cost. Drive process improvement and problem solving through Lean / Six Sigma principles and root cause analysis. Establish a collaborative working relationship with his/her Business Unit connections. Assess and evaluate facility maintenance personnel and make recommendations to the Operations Manager regarding strategies to remedy training, skills, or performance deficiencies. Provide direction, assistance, and resources necessary to inventory, organize and control MRO spares. Establish optimal spares inventory levels to ensure effective maintenance operation. Effectively utilize MP2 maintenance software to drive preventive and predictive maintenance activities. This will include tracking and analysis of work order performance, development of detailed PM tasks and schedules, and analysis of breakdowns and failures. Manage all outside service contractors. Ensure contractor compliance with plant safety requirements. Initiate, write, manage, and effectively lead the process for Capital Expenses. Construct, evaluate and report out maintenance and engineering results for the facility. <