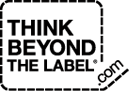
Job Information
Alamo Group Inc. Manufacturing Engineer in Wooster, Ohio
Join our growing team in Wooster, Ohio!
Formerly known as Rayco Manufacturing, and now part of the Alamo Group Snow & Ice Team, we manufacture heavy duty snow and ice removal equipment.
The Manufacturing Engineer will implement new equipment, processes, procedures and systems to produce Alamo Snow and Ice equipment. Develops and improves manufacturing processes/systems to improve production efficiency to reduce production issues and costs, while ensuring products meet established quality standards. Identifies and determines the most cost-effective processes, methods, systems, tooling, equipment and plant layout to be used in manufacturing. Evaluates labor and operating costs for compliance with standards and stated cost objectives develops short and long term manufacturing strategies and capital requirements, and actively participate in the development and introduction of new products.
Essential Functions of the Job:
Evaluates manufacturing processes by designing and conducting research applying knowledge of product design, fabrication, assembly, tooling, and materials; conferring with equipment vendors; soliciting observations from operators.
Develops manufacturing processes by studying product requirements; researching, designing, modifying, and testing manufacturing methods and equipment.
Improves manufacturing efficiency by analyzing and planning work flow, space requirements, and equipment layout.
Assures product and process quality by designing testing methods including fixtures and tooling; testing finished- product and process capabilities; establishing standards; confirming manufacturing processes.
Provides manufacturing decision-making information by calculating production, labor, and material costs; reviewing production schedules; estimating future requirements.
Prepares product and process reports by collecting, analyzing, and summarizing information and trends.
Keeps equipment operational by coordinating maintenance and repair services; following manufacturer's instructions and established procedures.
Completes design and development projects by training and guiding production team members.
Analyze engineering designs, procurement procedures, methods, time standards, machine utilization, material routing and handling methods, tool design and application, etc. to seek improvement and effect changes to reduce costs.
Prepare detail and fixture drawings; set up specifications and other pertinent design data for layout drawings.
Test all equipment for safety and effectiveness.
Research and test design ideas to determine feasibility, utilizing Lean Manufacturing, Kaizen, Six Sigma, and root cause analysis to formulate/support innovation, corrective actions, and continuous improvement activities.
Create and maintain required manufacturing process documentation, including process flow charts, capacity and utilization studies, time and motion studies, standard work, cycle time analysis and line balancing.
Knowledge, Skills and Abilities (KSA’s):
Knowledge of production processes, costs, quality control, raw materials and other methods for maximizing the efficient manufacture and distribution of goods.
Advanced knowledge of machines and tools, their designs, uses, repair and maintenance.
Strong planning and project management skills with the ability to work well under pressure and manage multiple projects and priorities.
Ability to design and understand precision technical plans, blueprints, drawings and models.
Knowledge of the ways various systems interact and how changes in operations, the environment and other conditions will affect outcomes.
Ability to read, analyze and interpret professional journals, technical procedures, or time study data. Ability to write reports and standard documentation. Ability to effectively present information and respond to questions from groups of managers and other employees of the organization.
Ability to work with mathematical concepts such as probability and statistical inference, and fundamentals of plane and solid geometry and trigonometry. Ability to apply concepts such as fractions, percentages, ratios, and proportions to practical situations.
Ability to collect data, establish facts, and draw valid conclusions. Ability to interpret an extensive variety of technical instructions in mathematical or diagram form and deal with several abstract and concrete variables.
Requires the ability to operate various equipment to include a computer, stopwatch, and various office equipment.
Requires a good understanding of tool making and the manufacturing process.
Able to read and use all precision measuring devices and equipment including micrometers, tape measure, dial calipers and calculator.
Knowledge of welding techniques and symbols.
Knowledge and safe use of hand tools, forklift and overhead crane.
Knowledge and use of fabrication, machining, welding and assembly procedures/processes such as drill press, lathe, shears, brake press, etc.
Excellent mechanical aptitude/ability.
Excellent communication skills, both verbal and written. Ability to communicate with various levels within the organization.
Must be organized and possess the ability to multi-task.
Able to work independently and with a high degree of accuracy
ALAMO GROUP CORE COMPETENCIES:
Leading Change / Change Management: Ability to drive improvement of team, division, and corporate goals and objectives through people. Ability to balance change and continually strive to improve business performance.
Leading People / Teamwork: Ability to design and implement strategies which maximize employees’ potential and foster high ethical standards in meeting the team, division, and corporate objectives.
Communication: Ability to explain, advocate, and express facts and ideas in a convincing manner, and negotiate with individuals and groups internally and externally. The ability to develop internal and external networks and identify the issues that impact the work of the organization.
Business Acumen: Understands and interprets business financials and metrics, and utilizes latest business strategies. Focuses on outcomes and creates opportunities for success. Acquires and utilizes human, financial, material and information resources effectively.
Results Driven: Ability to make timely and effective decisions and produce results through planning and the implementation and evaluation of business metrics, systems, policies, and program; stressing accountability and continuous improvement.
Education and Experience:
Bachelor’s degree in manufacturing, industrial, mechanical, or related engineering field.
Minimum of 5 years heavy equipment manufacturing experience.
Experience implementing new products.
Experience in costed BOMs.
Experience in sourcing and working with vendors to obtain quality parts.
Proficient in Microsoft Office Suite.
Experience using SolidWorks and EPDM vault, preferred.
Previous work experience using ERP systems, preferably JD Edwards.
In-depth understanding of lean manufacturing principles.
Proficiency with analytical tools, workflow time study, and process balancing.
Alamo Group is proud to be an Equal Employment Opportunity, Affirmative Action employer. All qualified applicants will be considered without regard to race, national origin, color, religion, age, genetics, sex, sexual orientation, gender identity or expression, disability or veteran status. We maintain a drug-free workplace and perform pre-employment substance abuse testing (where permitted by law).