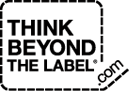
Job Information
DCL Corporation Maintenance Supervisor-Excellent opportunity! in Toronto, Ontario
GENERAL ACCOUNTABILITY
This is an excellent opportunity and to join the organization as a Maintenance Supervisor. With the appropriate skills. the salary is open to negotiation!
The Maintenance Supervisor's primary function is to maintain the New Toronto facility in a safe and efficient operating condition while meeting production objectives. Included in the maintenance activity is upgrading of equipment in poor repair or obsolete in nature.
Manage the responsibilities assigned to the position in both the Quality and Environmental (ISO) manuals.
Manage inventory of spare parts, purchasing all goods and services required by Maintenance department, supervisor of maintenance mechanics, coordination and supervision of contractors. Writing and management of requisitions for maintenance purchases and RFA (Request for Appropriation) for capital management and EOM (Extraordinary Maintenance).
NATURE & SCOPE
The Maintenance Supervisor reports directly to the Plant Manager and has approximately six direct reports.
The areas of control for the Maintenance Supervisor are:
Environmental, Health & Safety – the incumbent is responsible for maintaining the plant to operate to all standards and conditions put in place to meet Environmental, Health & Safety legislation. Upgrades have to include all the appropriate requirements for the Environmental, Health & Safety Acts. The incumbent has specific responsibilities for the Asbestos Management Program and for control of Maintenance generated waste.
Human Resources – the incumbent is responsible for ensuring all personnel reporting directly to him are trained and competent in job skills, Health & Safety, and ISO requirements. A complete understanding of the union relationship (contract) is required. Cooperation between the Maintenance group and other functions such as Production, Purchasing, Laboratory and office personnel is essential. Communication is an essential feature with all functions for a smooth transfer of information and ideas.
Technical – the assignments for the incumbent will require the use of mechanical trouble shooting and diagnostic procedures combined with his extensive plant knowledge and resourcefulness. Crisis management skills will also benefit the incumbent in times of emergency breakdown.
Engineering/Equipment – the Maintenance Supervisor maintains all equipment to optimum efficiency to support production targets and design conditions in a safe manner. The incumbent upgrades equipment and initiates improved maintenance practices. Engineering to be sourced from appropriate resources or consulted as required.
Maintenance Scheduling – the Maintenance Supervisor will plan maintenance shutdown and equipment repairs. Scheduling of preventative and predictive repairs as to minimize down time and liaison with production to perform repairs around production. Utilize and develop critical spare parts to minimize production delays.
Cost Control – the Maintenance Supervisor is accountable for control of maintenance labour costs and utilize efficient management purchasing practices.
Repairs – records and reports are to be maintained and kept on file. ISO records and preventative maintenance reports are to be filed centrally.
This position is responsible for having a working knowledge of health and safety, environmental legislation, including emergency response; and working knowledge of the ISO Quality System, relevant to DCC.
SPECIFIC ACCOUNTABILITIES
Maintain plant equipment in adherence with Environmental, Health & Safety regulations.
Maintain good working relationship with employees.
Ensure that employees reporting directly to this position are adequately trained and able to provide competent service.
Upgrade or replace obsolete equipment or equipment in poor repair.
Responsible for the implementation of predictive maintenance.
Maximize maintenance budget efficiency to maintain plant and equipment.
Organize maintenance shutdowns.
Consult with and maintain engineering standards.
Plan, purchase and stock all Maintenance Repair (MR) supplies and confirmation required for job completion.
Negotiate with suppliers for the goods and services.
Provide leadership and support for all maintenance personnel.
Implement cost saving strategies and techniques that will not compromise quality, individual safety and production objectives.
Other duties and responsibilities as assigned from time to time by the Plant Manager.
KNOWLEDGE / EDUCATION / EXPERIENCE
• Licensed Industrial Millwright with chemical process plant experience.
• Minimum of ten years experience in the successful performance of maintenance duties as a skilled technician in primarily the mechanical area with the ability to understand and troubleshoot electrical and instrumentation problems.
• Previous experience in the chemical industry environment is required.
• Working knowledge of fire protection codes, building and electrical codes, OSHA, environmental regulation and company requirement and knowledge of safe working techniques and procedures is essential.
• Ability to interact effectively with personnel at all organizational levels with specific ability to interact and communicate effectively at Maintenance Mechanic level.
• Ability to work independently with limited guidance and under pressure while continuously meeting deadlines.
WORKING CONDITIONS
A combination of office (frequent interruptions), maintenance shop and process plant exposure where protective clothing and equipment will be necessary. Working both inside and outside plant in all temperature and weather conditions. Job involves frequent standing and walking and the ability to react quickly to breakdowns while managing purchasing and scheduling functions.