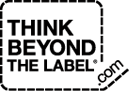
Job Information
West Pharmaceutical Services Tooling Engineer in St Petersburg, Florida
Tooling Engineer
Requisition ID: 68841
Date: Mar 17, 2025
Location:
St Petersburg, Florida, US
Department: Engineering
Description:
At West, we’re a dedicated team that is connected by a purpose to improve patient lives that has been at the center of our Company for more than a century. Our story began when Herman O. West solved the problem of supplying penicillin in mass quantities to the US Government during World War 2. Through our work to deliver thousands of life-saving and life-enhancing injectable medicines to millions of patients daily, West’s indelible mark on the healthcare industry has just begun. A name started our story. How will yours help write our future?
There’s no better place to join an inclusive community of professionals with opportunities for lifelong learning, growth and development. Supported by benefit programs, we empower the physical, mental, emotional and financial health of our team members and their families.
We believe in giving back to help those in need in the communities where we live and work. And are equally committed to creating a healthier environment and planet through our sustainability efforts.
Job Summary
In this role, you will coordinate/assign work and provide operational support in your area of responsibility for the construction and/or repair of molds, dies, and/or ancillary equipment. Oversee the set-up, tooling, programming, and operation of CNC and/or manual milling, turning, and grinding machines that facilitate mold and die component manufacture/assembly. Schedule projects into suitable machines. Ensure inspection methodologies are appropriate, repeatable, and capable of maintaining specifications within tolerances. Assist in documenting new and existing procedures throughout the facility. Investigate, recommend and apply appropriate technology enhancements. May support in designing tools the manufacturing facilities require for production.
Essential Duties and Responsibilities
Coordinate and assign work throughout the machine shop, including tooling construction, machine repairs/calibrations/maintenance in collaboration with the production planner and site manager. Provide operational support for team members and equipment.
Conduct performance management and related activities of those employees within your area of responsibility in coordination with site manager.
Ensure that all appropriate Quality Assurance procedures are followed. Accept responsibility for the quality of the work produced in the machine shop. May assume responsibility for various assigned projects to improve product quality and tooling designs.
Troubleshoot & remediate problems with existing production tooling at this facility &/or outlying plants. May work with cross-functional teams throughout all West locations to develop best practice standards.
Devise machining/assembly processes for tooling projects that minimize cycle time & maximize quality.
Develop & document new process procedures (in current SOI format) in collaboration with manufacturing engineer and area SME’s. Assist in providing training for affected employees on the safe & effective use of those procedures.
Assess, improve, & document existing processes (in current SOI format).
Develop specific objectives and manage work assignments with guidance to achieve personal objectives in conformance with overall business goals. Able to identify gaps in the department and fill them to support the department.
Maintain effectiveness when experiencing major changes in work responsibilities or environment; adjusting effectively to work within new work structures, processes, requirements, or cultures.
Additional Responsibilities
Challenge processes, remain open to ideas and changes to continuously improve, seek better alternatives, and drive change.
Lead Continuous Improvement teams & ensure timely completion of projects. Provide quality feedback to appropriate team members to support Continuous Improvement.
Help and instruct fellow employees as needed & assist in the orientation & training of new employees.
Coordinate equipment maintenance per vendor/West maintenance schedule.
Document drawing changes (ECNs), inspection results, etc. as needed per West & cGMP requirements in collaboration with QA manager and manufacturing engineer.
Collaborate with the global tooling team (TLCM, Design, Bodmin and German tool shops) on tooling and manufacturing issues. Collaborate with production plant stakeholders on repairs and tooling related issues.
Observe all plant safety rules, regulations and HSE policies. Maintain compliance with all HSE policies and procedures for all team members.
Keep equipment & working areas in a clean & orderly condition.
May maintain and support existing tooling and coordinate tooling orders for manufacturing plants.
May implement innovative solutions to meet or exceed customer quality expectations. Maintain awareness of new technology trends, materials, and design/analytical software and able to design experimental molds, commercial molds, MTD´s and devices.
May write engineering studies and technical reports to support tool designs and features.
Other duties as assigned.
Education
High School Diploma with 10-15 years related manufacturing (precision machining) experience required or
Associate's Degree with 5-10 years related manufacturing experience (or equivalent education / training / experience); required or
Bachelor's Degree with 5+ years manufacturing experience required
Work Experience
Preferred Knowledge, Skills and Abilities
#N/A
License and Certifications
Travel Requirements
5%: Up to 13 business days per year
Physical Requirements
Medium-Exerting up to 50lb/22kg of force occasionally and/or up to 20lbs/9kg of force frequently, and/or up to 10lbs/4kgs of force constantly to move objects.
Additional Requirements
Frequent standing, twisting, bending, reaching, pushing, pulling and walking.
Must have excellent organizational interpersonal and problem-solving skills and be able to interface with employees in all levels of the organization and in a variety of situations.
Effective personal time management skills and must be able to multi-task, work under time constraints, and prioritize with constant interuptions.
Must have the cognitive ability to plan, execute to goal, supervise and coordinate the work of a team in area of responsibility.
Ability to quickly adapt to changes in a dynamic environment.
Must be able to maintain confidentiality and effectively resolve conflicts.
Able to routinely use standard office equipment such as computers, phones, photocopiers, filing cabinets and fax machines. Position operates in a professional office environment. May stand or sit for extended periods of time.
Leadership skills and must be able to communicate effectively with written and oral skills, make quick decisions, interpret data, read and write, speak in front of groups, express and exchange ideas, understand direction and adhere to procedures.
Read and interpret data, information and documents.
Observe and interpret situations, analyze and solve problems.
Ability to make independent and sound judgments with guidance from management as needed.
#LI-TH1
West is an equal opportunity employer and we value diversity at our company. We do not discriminate on the basis of race, religion, color, national origin, gender, sex, gender identity, sexual orientation, age, marital status, veteran status, or disability status. If you have a special need that requires accommodation in order to apply to West, please send an email to Apply.Accommodation@westpharma.com . Where permitted by law, an offer of employment with West Pharmaceutical Services, or any of its subsidiary or affiliate companies, is contingent upon the satisfactory completion of background screening and/or a pre-employment drug screening.