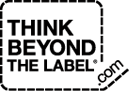
Job Information
Boulder Scientific Company Manager, Maintenance & Facilities in Mead, Colorado
Manager, Maintenance & Facilities
Mead, CO
Full Time
Maintenance
Manager/Supervisor
Share (https://boulderscientificcompany.applytojob.com/app/share/PVo6lJiLT1)
Boulder Scientific Company (BSC) is headquartered in Mead, CO, and is a premier provider of organometallic compounds and other specialty chemicals used in a wide range of applications. BSC is a pioneer and leading manufacturer of metallocene catalysts and co-catalysts that are primarily used to produce metallocene polyethylene, polypropylene and elastomers,but also supplies products into Electronics, Pharmaceutical and Defense applications.BSC operates two sites in Northern Colorado, which include: a main production facility in Mead and a second facility in Longmont. BSC has continuously grown the sales of its products to existing and new customers and expects to continue on a high growth trajectory.
Pay for this role is $120,000-135,000 annually, depending on experience. BSC offers medical, dental, vision, flexible spending, and 401(k) with matching. See more about our offerings on ourOpportunities (https://www.bouldersci.com/opportunities/) page.
Boulder Scientific Company is an Equal Opportunity Employer/Veterans/Disabled.
We are seeking a knowledgeable Industrial Maintenance and Facilities Maintenance Manager to oversee and maintain multiple production facilities, laboratories and offices. ThePrimary responsibility of this role is lead, train and develop the maintenance team and maintenance program for all facilities, labs and plant manufacturing machinery including but not limited to Reactors, pumps, agitators, compressed air system, boilers, Cooling Towers, HVAC/chillers, water systems, electrical systems, etc.
Top Five Broadly defined Responsibilities
Safety
Team Leadership and Development/Training
Planning, scheduling and executing Maintenance activity and Compliance Activity in a timely manner
Tracking and presenting KPIs for maintenance performance, maintaining departmental budgets, and personnel
Plan/Schedule/Lead Annual Plant Turn-around
Leadership Behaviors
Leads by giving and earning trust
Demonstrates ethical behavior; strives to meet and exceed our Environmental and Safety requirements
Acts respectfully, demonstrates the ability to Listen, Think, Speak (in that order)
Is Accountable: holds self and others accountable
As a leader, demonstrates his/her most important values visibly everyday while at work
Job Responsibilities
Oversee, manage, and document all day-to-day multiple site activities performed by Maintenance personnel
Support compliance efforts with local, state, and federal regulations concerning environmental affairs, OSHA, NFPA, DHS, and other governing agencies
Recruit, select, hire, develop and continuously train Maintenance Technicians; coach to improve performance; hold technicians accountable for meeting established goals
Work with multiple internal customers to minimize business disruptions while maintaining equipment and performing critical tasks
Utilize, maintain and mature the CMMS system (Asset Essentials) to build a robust time-based and condition-based maintenance program
Equipment criticality
Work order criticality
Work load leveling
Labor utilization / time writing
Materials utilization / Materials costs
Properly planned work packs and work plans
Monitor and maintain maintenance inventory and critical spare inventory
Capture root causes of failures and corrective actions for posterity
Utilize proper skilled techniques to assure the safe and efficient operation of all plant machinery
Assist the PSM Manager in creating a strategic plan to migrate site to PSM standards for all equipment
Function as a project manager for small maintenance and small capital projects such as concrete slab, building construction, reactor replacements, etc.
Schedule subcontractors and material/equipment deliveries; ensure the BSC teams and subcontractors have the necessary project resources, a safe project site, and support to assure success of all team members
Develop a structure that includes maintenance assignments to various activities:
Fabrication Shop
Mead Production and Pilot Plant
Mead support facilities
SP Production
SP support facilities
Cactus office facilities
Work in conjunction with the Production Planner to coordinate maintenance activities with available equipment or scheduling equipment to be available for required maintenance
Maintain close coordination with production department to resolve equipment breakdowns and other production-related opportunities
Support an environment of continuous improvement by making/implementing suggestions
Set up and maintain a housekeeping plan for the areas assigned to Maintenance
Develop the staffing plan to assign personnel to 7 days per week operation
During turnarounds or major shutdowns, schedule subcontractors and material/equipment deliveries
Coordinate activities with the Construction Manager for major, subcontracted projects
Communicate and coordinate with the equipment suppliers to resolve plant equipment related issues
Lead the Facilities Committee with the goal to maintain, repair, or replace equipment when necessary seeing to timely basic plumbing, mechanical, and electrical, and building repair work when necessary
Lead Committee on assigning seating, updating spaces, and acquiring need space as needed
Participate in Hazops, pre-startup safety reviews, CAPAs, and Failure Mode Effect Analysis (FMEA)
Drives own vehicle between BSC sites
Qualifications and Experience for the role
High School Diploma or GED required
8-12 years of demonstrated Industrial Maintenance / Mechanical Integrity / Manufacturing leadership experience required, preferably in a chemical, pharmaceutical, or similar industry containing industrial, manufacturing, laboratory and office facility oversight
Leadership experience in a manufacturing organization with multiple site responsibility and demonstrated management and compliance experience comprised of one or a combination of the following areas: facilities maintenance, plant engineering, PSM Mandated Process equipment and Mechanical Integrity programs, capital and overhead budget planning, leading employees, cost control, budgeting, and management systems and programs revolving around continuous improvement, and predictive and preventative maintenance leading to improved OEE
Demonstrated knowledge of required codes (API, ASME, OSHA, PSM, etc.)
Ability to read electrical wiring diagrams, control logic, P&IDs, Isometric drawing, blueprints, vendor drawings, and mechanical drawings
Proven facilities leadership experience with an organization supporting technical operations and equipment maintenance related to GMP or Fine Chemical manufacturing, test labs, clean rooms, and complex building support systems
Demonstrated mechanical and electrical aptitude
CMRP, PMP and/or other relevant Maintenance accreditation or degree preferred
Proficiency in Microsoft Office, proficiency with and development of CMMS required (Asset Essentials specifically preferred)
Must pass a job-related physical
Work Environment
The employee will be working indoors and outdoors in Colorado weather. The employee must frequently lift and/or move up to 10 pounds and occasionally lift and/or move up to 25 pounds. The employee will be walking and driving around and between BSC sites. The employee will be working in laboratories, manufacturing areas, and storage facilities that require the use of PPE.