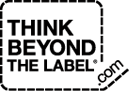
Job Information
TE Connectivity EMEA Manufacturing Engineer - Assembly in KURIM, Czech Republic
EMEA Manufacturing Engineer - Assembly
TE Connectivity is a global industrial technology leader creating a safer, sustainable, productive, and connected future. Our broad range of connectivity and sensor solutions enable the distribution of power, signal and data to advance next-generation transportation, renewable energy, automated factories, data centers, medical technology and more. With more than 85,000 employees, including 8,000 engineers, working alongside customers in approximately 140 countries, TE ensures that EVERY CONNECTION COUNTS. Learn more at www.te.com
TE Connectivity's Manufacturing Engineering Teams are process leaders for stamping, molding or assembly related topics, ensuring the processes are running at optimum levels for quality and output. They are experts in mold tooling, die tooling, machining, and assembly techniques, possessing extensive knowledge of the associated manufacturing processes which may include the optimization and standardization of stamping / molding / assembly or other processes within the manufacturing environment. Manufacturing Engineering Teams enable the TE business unit plants to reach TE Operating Advantage (TEOA) requirements, roll out Centers of Excellence (COE), Best Demonstrated Practices (BDP’s) and advise plants on tool and machine duplications / corrections / improvements. They design and develop manufacturing process and automation platforms and apply them for the realization of new product developments as well as optimization of existing products already in production. The Teams also support Product Development in the selection and optimization of tools for piece part production and the selection of the most suitable manufacturing concepts relative to planned manufacturing quantities, quality requirements and manufacturing location. They act as interface between engineering and production to ensure manufacturability of new designs and smooth production ramp up as well as support the research & development teams to produce sample manufacturing equipment, product samples and prototypes.
Job description:
Develop, update and own the safety retrofit roadmap and Overall Equipment Utilization (OEU) improvement roadmap for Assembly EMEA
Analyse assembly equipment safety levels and conditions, identify gaps, and drive gap closure plans
Analyse assembly equipment load and utilization, identify and drive opportunities for load increase, load switch, and balancing
Lead a cross-functional team for the Safety retrofit process and the Aftermarket process in Assembly EMEA
Prepare proposals for management decision in the areas of safety retrofit, including CAPEX estimation, timing, and priority definition
Prepare proposals for management decision regarding new sustaining projects launch (e.g., new lines for consolidated load, new conv. kits) and assembly equipment scrapping
Collaborate with ME, EHS and external equipment manufacturers on new machine safety standards
Collaborate with ME and Center of Excellence teams on potential new platforms and concepts aimed at improving assembly equipment load and utilization
Lead regular plant reviews regarding safety retrofit programs
Lead regular plant reviews in the areas of OEU and efficiency improvements
Regular reporting to the senior leadership team in the areas of safety retrofit and OEU improvement
Search, justify and deploy best-in-class solutions from internal and external sources to maintain a state-of-the-art assembly technology environment
Requirements:
University degree or technical degree in mechanical engineering or similar disciplines preferred
At least 3-5 years of experience in assembly processes or manufacturing engineering, eventually LEAN
Experience in cross-plant project management
Practical experience in machine safety, knowledge of the respective legal and TE requirements
Experience in machine performance KPI (e.g. OEE, OEU)
PC skills (MS Office), knowledge in SAP and Hydra preferred
Lean mindset and experience, formal Lean certifications (e.g. SS GB, Kaizen facilitator, Lean practitioner) is preferred
Innovative and high level of creativity among others to indicate trends and long-term development needs
Experience in leading cross-functional teams
Excellent communication skills, flexibility, persuasive personality and teamwork skills with analytical and structured thinking
English language skills, spoken and written
Presentation skills
Mobility and willingness to travel
Think bigger & smarter (innovative, out of the box)
We are pleased to offer you an exciting total package that can also be flexibly adapted to changing life situations - the well-being of our employees is our top priority!
Competitive Salary Package
Performance-Based Bonus Plans
Health and Wellness Incentives
Community Outreach Programs / Charity Events
Employee Resource Group
Across our global sites and business units, we put together packages of benefits that are either supported by TE itself or provided by external service providers. In principle, the benefits offered can vary from site to site.
Location:
KURIM, 623, CZ, 664 34
City: KURIM
State: 623
Country/Region: CZ
Travel: 25% to 50%
Requisition ID: 121806
Alternative Locations:
Function: Engineering & Technology
TE Connectivity and its subsidiaries, affiliates, and operating units (collectively, the "Company") is committed to providing a work environment that prohibits discrimination on the basis of age, color, disability, ethnicity, marital status, national origin, race, religion, gender, gender identity, sexual orientation, protected veteran status, disability or any other characteristics protected by applicable law or regulation.