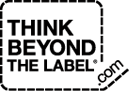
Job Information
J&J Family of Companies Quality Engineer in Gelderland, Netherlands
Quality Engineer - 2406179632W
Description
GATT Technologies, a Johnson & Johnson company based in Nijmegen, is currently seeking a highly skilled and experienced professional to join our team as Quality Engineer within the Quality department.
About the Company:
GATT Technologies BV is part of Ethicon, member of Johnson & Johnson MedTech.
GATT Technologies is specializing in the development and production of cutting-edge hemostatic products, including ETHIZIA hemostatic seal patch. As part of Ethicon, GATT Technologies is dedicated to shape the future of surgery through its commitment to help address the world’s most pressing health care issues and to deliver innovation to improve and save more lives. For more information, visit www.ethicon.com .
Use quality engineering principles to develop, optimize, and support systems and processes that are aligned with the overall Company strategy and mission affecting continuous quality improvement. Apply appropriate risk management to prevent unanticipated failure modes and improve capability of processes. Ensure compliance with company policies and procedures such as Design Control, Process Validation, Test Method Validation, and Sampling Plan Development and Review. Generates quality indicators and supports nonconformance investigation and corrective action implementation at the business unit level. Ensure QMS compliance.
Duties and Responsibilities
In accordance with all applicable federal, state and local laws/regulations and Corporate Johnson & Johnson, procedures and guidelines, this position:
Support, consult, train and lead quality improvement projects throughout the life cycle of Ethizia product, including product design and development, manufacturing, purchasing, and improvements.
Apply quality engineering tools and techniques to establish sampling plans, develop quality plans, conduct and participate in FMEA activities.
Conduct investigation, bounding, documentation, review and approval of non-conformances, CAPAs and customer complaints. Escalation of quality issues as appropriate.
Demonstrate independent understanding and application of core GMP fundamentals, such as: Data Integrity (DI), Good Manufacturing Practices (GMP), and Good Documentation Practices (GDPs).
Develop, write and approve policies, procedures, test methods, specifications.
Assess the need for risk mitigation techniques given product classification, potential defect types, defect frequency, severity, patient risk, process capability, process controls, etc. Assess whether a proposed change to a process will not increase the risk level in some way beyond capability of current controls or whether change will result in potential non-compliance.
Assist with establishing validation and /or qualification policies. Assist in identification of validation problems for equipment and /or performance processes and develop, review and/or supervise execution of validations documentation (eg. IQ, OQ, PQ and verification studies).
Ensures that software validations are performed according to applicable FDA guidelines. Provides end user support by software validation throughout the Software Validation Life Cycle.
Support External and Internal audit. Lead or act as team member of audit observation investigation and action plans.
Collect data, conduct various analytical/statistical analysis and interpretation, prepare reports and provide information as part of process improvements and day-to-day support.
Maintain compliance of quality records and QMS associated systems, including but not limited to Records management process and PLM system.
Provide Training/Consultation on quality concepts, quality technology tools, nonconformance and investigations.
Responsible for communicating business related issues or opportunities to next management level.
Responsible for following all Company guidelines related to Health, Safety and Environmental practices as applicable.
For those who supervise or lead a staff, responsible for ensuring that subordinates follow all Company guidelines related to Health, Safety and Environmental practices and that all resources needed to do so are available and in good condition, if applicable.
Responsible for ensuring personal and Company compliance with all Federal, State, local and Company regulations, policies, and procedures.
Performs other duties assigned as needed.
Qualifications
Experience and Education
Bachelor’s degree in engineering, science, mathematics or statistics is required.
A minimum of two years related manufacturing experience and/or training; or equivalent combination of education and experience is desired.
Knowledge of good manufacturing principles and practices, and procedures.
Required knowledge, skills, abilities, certifications/licenses and affiliations
Knowledge of ISO13485 and cGMP regulations is required.
An ASQ certification (CQE, CQM, CRE or CQA), Six Sigma (Green Belt, Black Belt, etc.) or Process Excellence certification is preferred.
Ability to work on multi-functional teams and to communicate proficiently within diverse interdepartmental groups is required.
Technical training and experience using Statistics, Lean and/or Six Sigma Methodologies is preferred.
The ability to perform "hands on" troubleshooting and problem solving is required. Good technical understanding of manufacturing equipment and processes is required.
Ability to periodically work with associates and processes in a special environment such as a Controlled Manufacturing Environment is required. This position will involve periodic entry into Controlled Manufacturing Environment production environment which requires certain preparation and gowning practices.
Additional position requirements
Ability to occasionally work in a Controlled Manufacturing Environment.
Ability to wear protective garb such as lab or clean room gowns.
Responsibility for others & internal interactions
This position reports to the Senior Quality Engineer.
Works in collaboration with all other departments to ensure quality and compliance aspects are incorporated and maintained related to quality engineering and validation.
External interactions
- The position may require interactions with government agencies, competent authorities, third part suppliers or customers of J&J. For more than 130 years, diversity, equity & inclusion (DEI) have been part of our cultural fabric at Johnson & Johnson and woven into how we do business every day. Our commitment to respect the dignity and diversity of all is embedded in our Credo. We know that the success of our business depends on having the best talent in a workforce that reflects the diverse markets we serve around the world and an inclusive culture that values different perspectives and life experiences That is why we are working to create an inclusive environment where diverse backgrounds, perspectives and experiences are valued and each and every one of our people feels that they belong and can reach their potential. No matter who they are. Diversity, Equity & Inclusion at Johnson & Johnson means “You Belong”!
Primary Location Europe/Middle East/Africa-Netherlands-Gelderland-Nijmegen
Organization 8354-GATT Technologies B.V. Legal Entity
Job Function Quality Engineering
Req ID: 2406179632W