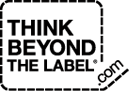
Job Information
Associated Milk Producers, Inc. MAINTENANCE TECHNICIAN in Freeman, South Dakota
Description
JOB SUMMARY: Ensures that all equipment is operating effective and efficiently, must have excellent proficiency in PM's, over-hauls, modification, fabrication, and welding, medium electrical repair. Must have the ability to adjust devices and control instrumentation, able to read electrical and mechanical blue prints. Working knowledge of machine shop equipment, excellent trouble shooting and problem solving skills. In addition, all technicians are expected to work on any assignment-determined necessary by the Maintenance Manager or management to ensure team success. ESSENTIAL RESPONSIBILITIES: This list of duties and responsibilities is not all inclusive and may be expanded to include other duties and responsibilities as management may deem necessary from time to time. 1. Ensures safe operations through adherence to Environmental, Health, and Safety programs and procedures. 2. Strict adherence to housekeeping, cleans work areas upon completing a project and plant GMPs. 3. Provide maintenance support to all stations effectively and efficiently. Quick response to maintenance related issues, quickly resolve problems, and make necessary adjustments as needed to maintain safety, product integrity and production efficiencies. 4. Diagnose, install, and repair all plant systems. 5. Ensures operation of plant equipment by completing preventive maintenance requirements on motors, pneumatic tools, conveyor systems, and production machines; following diagrams, sketches, operations manuals, manufacturer's instructions, and engineering specifications. Responsible for the startup, operations, shutdown and basic maintenance to ensure operations of plant equipment. 6. Locates sources of problems by observing mechanical devices in operation; listening for problems; using precision measuring and testing instruments. Removes defective parts by dismantling equipment; using hand and power tools, cranes and hoists when necessary, and completing root cause analysis of parts. 7. Adjusts functional parts of devices and control instruments by using hand tools, levels, plumb bobs, straightedges. Determines changes in dimensional requirements of parts by inspecting used parts; using rules, calipers, micrometers, and other measuring instruments. 8. Conserves maintenance resources by using equipment and supplies as needed to accomplish job results. Anticipates needed equipment, parts, and supplies; placing and expediting orders; verifying receipt. 9. Demonstrate a cooperative effort to train and assist operators and peers in all aspects of equipment maintenance and operation, problem identification, and problem solving skills. 10. Controls downtime by informing production workers of routine preventive maintenance techniques; monitoring compliance. Documents downtime concisely, document problems and what corrective actions were taken. 11. Interact with vendors and suppliers to ensure efficient repair, parts stocking, and maintenance of plant equipment and systems. 12. Aid in the development of maintenance projects, assemble the bill of materials, and work with management on upgrades and modifications for plant enhancement. 13. Participate in task meetings; suggest changes in work tasks and use of equipment to increase efficiencies. 14. Function as an engaged team member and contribute to the site's continuous improvement efforts. 15. Follow all AMPI GMP's and work in a manner consistent with all corporate and regulatory, food safety, quality and sanitation requirements. 16. Able to effectively and safely operate standard maintenance tools such as power tools, basic hand tools, and basic electrical test meters. 17. Perform pneumatic, hydraulic system troubleshooting, and repairs. 18. Troubleshoot and repair of mechanical and electrical related issues without direct supervision. 19. Effectively pass-down to next shift personnel, unfinished repairs and unresolved maintenance/production issues. 20. Ability to read and omprehend standard operating procedures and company guidelines in order to maintain regulatory compliance. 21. Partake in the Emergency Response program is required. 22. Assists with training new employees; 23. Adhere to all Quality and Food Safety policies and procedures, reporting any nonconformity 24. Adhere to all Safety policies and procedures, reporting any nonconformity 25. Adhere to all GMP policies and procedures, reporting any nonconformity An individual in this position must be able to successfully perform the essential duties and responsibilities listed above. Reasonable accommodations may be made to enable individuals with disabilities to perform the essential functions of this position. The above list reflects the general details necessary to describe the principle and essential functions of the position and shall not be construed as the only duties that may be assigned for the position. REQUIRED COMPETENCIES: The following are required competencies of the position that must be met by the employee to successfully perform the essential functions of the job: * Use graphic instructions, blueprints, schematic drawings, layouts, or other visual aids. * Observe or monitor objects such as mechanical devices to determine compliance with prescribed operating or safety standards. * Understand and follow written and oral instructions in the English language. * Knowledge of Occupational hazards and necessary safety precautions applicable to mechanical maintenance and repair work, including lockout procedures and confined space entry procedures. * Deals with uncertainty, attention to detail, a sense of urgency, flexibility, able to perform with little supervision, job knowledge, and reliability, honest, able to communicate effectively. * Understand and follow written and oral instructions in the English language. * Must have proven working knowledge of electrical/mechanical skills and have operational knowledge of basic tools and equipment. PLC experience a plus. * Must be able to demonstrate an ability and willingness to communicate effectively in order to maintain high levels of Safety, Quality and Efficiency * Ability to read and comprehend standard operating procedures and company guidelines in order to maintain regulatory compliance * Participation in a team environment safely * Detail oriented, be quality minded * Able to perform at a high level in a fast paced environment * Completion of respirator fit testing and training is required.
EDUCATION / EXPERIENCE:
- High School Diploma or General Education Degree (GED) is preferred
- Prior maintenance experience in the dairy industry is preferred
- 1- 2 years of skilled experience in mechanical maintenance and repair work. Other combinations of experience, with prior experience in a food manufacturing environment, a plus.
- Knowledge of HACCP, GMP's, OSHA and loss control programs is highly desirable
- Experience with PLC's, electrical, Ammonia, Boilers, and welding is preferred.
PHYSICAL DEMANDS AND WORK ENVIRONMENT: The physical demands described here are representative of those that must be met by an employee to successfully perform the essential functions of this job. Reasonable accommodations may be made to enable individuals with disabilities to perform the essential functions. * Physical Demands - Employee is frequently (more than 75% of time) required to: use hands to finger, handle, or touch objects, tools, or controls, sit; to verbally communicate; and to hear. The employee is frequently (up to 90% of the time) required to walk and stand. The employee must frequently (up to 50% of the time) lift and/or move up to 50 pounds and be able to lift and/or move 75 pounds occasionally. Specific vision abilities re