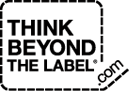
Job Information
SCHOTT North America, Inc. Head of Production in Duryea, Pennsylvania
Reference #: 83847-en_US About us
Your Contribution
Planning: Develops budget-, personnel- and investment planning on the basis of long-term department planning. Prepares long-term shift and staffing plans in conjunction with subordinate managing body. Production: Ensures the on schedule and appropriate production in consideration with cost aspects, quality requirements and customer demands. Develops production instructions and production schedules. Verifies shift reports to locate trends, deviations and disorders. Decides on actions in case of significant interferences. Repair and Maintenance: Ensures continuous maintenance of production equipment. Executes special inspections in case of machine faults to locate causes of failure. Arranges the execution of repairs by to internal or external bodies. Development: Informs about new technological developments. Submits proposals to improve manufacturing facilities. Executes and examines the testing of new pilot facilities/equipment and new manufacturing methods. Decides on the implementation of new methods as well as the use and purchase of new production facilities. Supervision: Leads, promotes, and motivates the employees within his/her area of responsibility (especially performance appraisal and goal setting agreement, successor and representative planning, personnel development and training measures). IMSU/ EHS: Ensures adherence to and monitoring of legal laws and internal regulations concerning IMSU/EHS in his/her organizational unit and is occasionally involved in the development of new concepts and directives in close corperation with the IMSU/EHS site advisor. Ensures implementation of the concepts in his/her area of responsibility and takes care of the corresponding instruction and training of his/her employees. Lean-Manufacturing: Designs processes according to the principle of Lean Manufacturing and ensures that these are executed and observed in his or her organizational unit. Makes sure that the manufacturing environment fully understands the idea behind Lean Manufacturing and registers employees for training courses and/or activities aimed at refreshing skills. Sees to it that SCHOTT standards are applied in the area of Lean Manufacturing when new personnel are hired and with transfers. Registers employees for mandatory training courses and offers additional dedicated training measures, if necessary. Informs himself or herself of the current training offerings on a regular basis. Keeps himself or herself aware of new developments in the area of Lean Manufacturing by participating in advanced training courses.
Your Profile
Degree in Mechanical Engineering
6-8 years of experience in the area of melting, hot forming and post-processing of glass, Management experience, Lean Manufacturing or similar concepts in production and close to production areas (maintenance, repair, logistics)
Good Command of the English language, extensive Lean knowledge which includes 5S methods, value stream analysis, etc. (lean-modules 1, 2, 3*, if required); Optional: SixSigma, In addition: basics in IMSU/EHS
Your Benefits
SCHOTT's openness to promote your further development is just as great as our additional benefits. Ranging from active health management via flexible working hours and hybrid work all the way to corporate pension plans: everything geared to suit your goals and needs. Discover a special corporate culture where everyone has the opportunity to develop their entire potential. At SCHOTT, you can expect a unique corporate culture where we emphasize equity, diversity, and inclusion. We know: motivated and committed employees are the precondition for the success of our company. 401(k) Plan; Free Parking; Medical, Dental and Vision coverage; Talent development; Tuition Reimbursement; paid vacation days, holidays and sick time
Please feel free to contact us
Your Profile
Degree in Mechanical Engineering
6-8 years of experience in the ar a of melting, hot forming and post-processing of glass, Management experience, Lean Manufacturing or similar concepts in production and close to production areas (maintenance, repair, logistics)
Good Command of the English language, extensive Lean knowledge which includes 5S methods, value stream analysis, etc. (lean-modules 1, 2, 3*, if required); Optional: SixSigma, In addition: basics in IMSU/EHS Your Contribution
Planning: Develops budget-, personnel- and investment planning on the basis of long-term department planning. Prepares long-term shift and staffing plans in conjunction with subordinate managing body. Production: Ensures the on schedule and appropriate production in consideration with cost aspects, quality requirements and customer demands. Develops production instructions and production schedules. Verifies shift reports to locate trends, deviations and disorders. Decides on actions in case of significant interferences. Repair and Maintenance: Ensures continuous maintenance of production equipment. Executes special inspections in case of machine faults to locate causes of failure. Arranges the execution of repairs by to internal or external bodies. Development: Informs about new technological developments. Submits proposals to improve manufacturing facilities. Executes and examines the testing of new pilot facilities/equipment and new manufacturing methods. Decides on the implementation of new methods as well as the use and purchase of new production facilities. Supervision: Leads, promotes, and motivates the employees within his/her area of responsibility (especially performance appraisal and goal setting agreement, successor and representative planning, personnel development and training measures). IMSU/ EHS: Ensures adherence to and monitoring of legal laws and internal regulations concerning IMSU/EHS in his/her organizational unit and is occasionally involved in the development of new concepts and directives in close corperation with the IMSU/EHS site advisor. Ensures implementation of the concepts in his/her area of responsibility and takes care of the corresponding instruction and training of his/her employees. Lean-Manufacturing: Designs processes according to the principle of Lean Manufacturing and ensures that these are executed and observed in his or her organizational unit. Makes sure that the manufacturing environment fully understands the idea behind Lean Manufacturing and registers employees for training courses and/or activities aimed at refreshing skills. Sees to it that SCHOTT standards are applied in the area of Lean Manufacturing when new personnel are hired and with transfers. Registers employees for mandatory training courses and offers additional dedicated training measures, if necessary. Informs himself or herself of the current training offerings on a regular basis. Keeps himself or herself aware of new developments in the area of Lean Manufacturing by participating in advanced training courses.
SCHOTT North America, Inc. is an Equal Opportunity/Affirmative Action Employer. Applicants considered without any regard to race, color, creed, religion, age, national origin, ancestry, ethnicity, gender, gender identity, gender expression, sexual orientation, marital status, veteran status, disability, genetic information, citizenship status or membership in any other group protected by federal, state or local law. Any form of unlawful harassment is prohibited.
Wages negotiable depending upon experience.