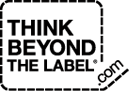
Job Information
Abbott Process Operator in Cootehill, Ireland
About Abbott
Abbott is a global healthcare leader that helps people live more fully at all stages of life. Our portfolio of life-changing technologies spans the spectrum of healthcare, with leading businesses and products in diagnostics, medical devices, nutritionals and branded generic medicines. Our 113,000 colleagues serve people in more than 160 countries.
Abbott serves the Irish market with a diverse range of healthcare products including diagnostics, medical devices and nutritionals products. In Ireland, Abbott employs o6,000 people across ten sites. We have six manufacturing facilities located in Clonmel, Cootehill, Donegal, Longford and Sligo and a third-party manufacturing management operation in Sligo. Abbott has commercial, support operations and shared services in Dublin and Galway. We have been operating in Ireland since 1946.
Abbott Ireland Nutrition Division Cootehill Cavan
Abbott Nutrition produces a range of infant formulae in all pack sizes under the brand name “Similac”. To complement the range of “Similac” infant formulae, the facility also manufactures a range of follow on formulae under the brand name of “Gain”. The essential ingredient is liquid skim milk and this is combined with carbohydrate, vegetable oils, vitamins and minerals. The product is blended, pasteurised, dried and packaged at the site and once packaged, is distributed to Europe, South East Asia, the Middle East, Latin America and Canada.
Established in 1975, Abbott Nutrition in Ireland is the largest powder manufacturing facility for the production of infant formulae within the Abbott Corporation worldwide. Approximately 1,000 dairy farms in Ireland and Northern Ireland supply quality milk to the Cootehill facility which processes 500,000 litres per day. This secure supply together with Ireland’s reputation as a green, clean environment is of significant strategic importance to Abbott Nutrition.
Primary Function
• Follow all Health and Safety Rules and Regulations in the plant.
• Report any current or potential hazards to the immediate shift co-ordinator/dept. manager immediately.
• Report all incidents accidents/near miss to your supervisor manager.
• Wear the correct Personal Protective Equipment (P.P.E.) at all times. Consult the appropriate SOP where required.
• Consult any SOP’s for any job task he/she may carry out and ensure they fully understand and adhere to the SOP.
• Ensure all housekeeping activities in the Packing Area are observed and carried out appropriately. Adhere to the Housekeeping SOP.
• Observe cGMP and quality as a main priority in any operation carried out in this job function.
• Follow the most up to date SOP which outlines the procedures for undertaking a line clearance in the Packing Area and the checks required before start-up of a new work order.
• Fill in data on OEE System for downtime in the area.
• Print off documents from the Teamcenter System when required.
• Print labels as required, and operate MCS System when required.
• Ensure compliant in all aspects of work.
• Contribute to business excellence programme.
• The operator must also check bill of materials for confirmation of requirements.
• Report any hazards, cGMP & hygiene failures to the Shift Manager.
• Carry out manual cleaning on all Packing areas per schedules in place.
• Actively work on own development and training with your manager.
• This Job function will change where update procedures to cGMP, EHS, Technical / New Equipment, Quality Procedures & SOP’s are made.
• Ensure the correct procedure is carried out when entering data or changing data in the printers for printing onto cartons, ink-jet can coders and can end emboss.
• Follow the most up to date SOP for Can End Coding & Videojet Can End Coder.
• When embossing, ensure that all clincher safety precautions are observed – outlined in relevant SOP.
• Use disposable latex or cotton gloves provided when handling inks or solvents.
• Can End Coding ensure the appropriate information appears on the can ends as per the most up to date SOP.
• Carton Coding ensure the information to be printed is divided up correctly from the work order printer and ensure that the carton coding is being completed as per the most up to date SOP.
• The operator must also check bill of materials for confirmation of requirements.
• Fill in data on OEE System for downtime in the area.
• This list of responsibilities may change depending on plant needs and employees are expected to be adaptable and flexible were this need arises.
Major Responsibilities
• Ensure all areas are kept clean and tidy at all times to ensure no non-compliance to cGMP or Hygiene rules and regulations.
• Ensure all documentation and records are maintained.
• Ensure cleaning is carried out per schedules in place.
• Ensure all Training requirements and SOPs are up to date.
• Monitor, control and carry out all operations relating to the Packing Line such as QA checks (Sediment, Leaker, Carton checks, Oxygen checks & other Packing line checks), scoop dropper/seamer, de-palletizer & can ends, clincher and gas box operations, involvo and all other operational requirements of the packing line as determined by your Manager
Supervisory/Management Responsibilities
• Not Applicable
Education Required
• Leaving Certificate.
Knowledge:
• Knowledge of the manufacturing process.
• Basic computer skills are required for documentation purposes.
• Good problem solving and communicational skills are required.
• Be familiar with Abbott Standards in relation to cGMP and Hygiene
Accountability / Scope
• On the packing line faulty caps should be rejected as they are not in compliance with customer requirement and do not meet the intended purpose. If bar code reader was not set to the correct operation it may result in faulty cans being sent to customers. Stickers inserts combi should be used as per specification and if this is not adhered to customer satisfaction is not met.
• Carry out the relevant packing line tests e.g. oxygen, sediment, carton and leaker checks etc.
• When operating the Clincher & Gas Box effects on product quality can occur if cans are not adequately subjected to gas mix. Damaged cans could go through the systems if not monitored accordingly.
• When operating the De-palletizer & Can Ends if there is a lapse in the supply of can ends and cans this can result in downtime.
• When operating the Scoop Dropper/Seamer dirt, oil, grease etc, on scoops can cause the product to be contaminated and therefore should not be distributed to customers. All can ends should be seamed per specification.
• When operating the Tavil if the cans are not packed properly or according to customer specification it can result in rejects, recall and non-conformance.
• Deviation from specification or failure to take corrective action or follow procedures for any period to time could have serious financial and quality consequences.
An Equal Opportunity Employer
Abbot welcomes and encourages diversity in our workforce.
We provide reasonable accommodation to qualified individuals with disabilities.
To request accommodation, please call 224-667-4913 or email corpjat@abbott.com