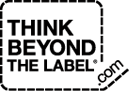
Job Information
TE Connectivity MANUFACTURING ENGINEER II in BANGALORE, India
MANUFACTURING ENGINEER II
At TE, you will unleash your potential working with people from diverse backgrounds and industries to create a safer, sustainable and more connected world.
Job Overview
TE Connectivity's Manufacturing Engineering Teams are process leaders for stamping, molding or assembly related topics, ensuring the processes are running at optimum levels for quality and output. They are experts in mold tooling, die tooling, machining, and assembly techniques, possessing extensive knowledge of the associated manufacturing processes which may include the optimization and standardization of stamping / molding / assembly or other processes within the manufacturing environment. Manufacturing Engineering Teams enable the TE business unit plants to reach TE Operating Advantage (TEOA) requirements, roll out Centers of Excellence (COE), Best Demonstrated Practices (BDP’s) and advise plants on tool and machine duplications / corrections / improvements. They design and develop manufacturing process and automation platforms and apply them for the realization of new product developments as well as optimization of existing products already in production. The Teams also support Product Development in the selection and optimization of tools for piece part production and the selection of the most suitable manufacturing concepts relative to planned manufacturing quantities, quality requirements and manufacturing location. They act as interface between engineering and production to ensure manufacturability of new designs and smooth production ramp up as well as support the research & development teams to produce sample manufacturing equipment, product samples and prototypes.
Responsibility:
• Analyze new technology and manufacturing processes. Plan and assess the feasibility of new and running automation projects.
• Troubleshooting skills and failure analyses for resolving problems of electrical and electronics, pneumatics and Hydraulics devices like Servo, PLC, HMI, Pneumatics.
• Hands on experience in robotic installation, commissioning.
• Implementing digital factory, cloud-based systems, AI Vision, AR/VR, IOT, Industry 4.0, Machine connectivity, Traceability Systems through wi-fi as well as wired network.
• Vendor management, Installation, and commissioning of new Equipment’s and co-ordinate with Vendor/CFT for complete process validation.
• New project conceptualization, Design, and development and machine buy-off and qualification.
• Develop new process and create all process documents like PFC, PFMEA, Control plan and SOP by understanding the depth of product requirements
• Prepare CT & Investment for new product and always work on to reduce cost by optimization/automating process to reduce cost.
• Responsible for ordering spares and vendor management, down time reduction
• Capacity & Layout planning/execution for new product line.
• Support manufacturing for Continuous Improvement, quality issues on the floor, new launches, engineering changes and Lessons Learnt.
• Develop and implement systems that optimize all phases of production process. Conduct Root-Cause Analysis.
• Review designs for manufacturing feasibility, suggest changes to the design to ensure product cost effectiveness
• Establish Tool management System (TMS), Calibration management, Document management Systems like Vicidocs, IQ-RM, Etc.
• Implement Process monitoring and Control (SPC & SQC), quality traceability Systems using IOT technology.
• Create, Maintain & Control all the programming software’s and production control documents for anytime ready for Auditing.
• Hands on experience on mechanical 3D design software’s like Creo, Pro-e or Solid works
Desired Candidate Profile:
EDUCATION/KNOWLEDGE
• BE/ B. Tech (Mechatronics, Electrical/Electronic or Mechanical/Instrumentation)
• Or Diploma with Good experiences.
• Knowledge on Connector & Harness is added advantage.
• 58 years related industry experience with good communication, stakeholder management. & Project management skills will be ideal
CRITICAL EXPERIENCE
• Should have worked in assembly industry with minimum 5+ years of experience in execution of automation projects and vendor management
• Experience in quality & productivity improvement projects (TPM)
• Experience in automation/robotics project execution and SPM’s
COMPETENCIES
• Operational Excellence: Ability to create strategy maps (X-Matrix) for manufacturing engineering function to meet plant goals, implement and execute actions as per the X-matrix.
• Industrialization focus: Capability to work with cross functional team for planning, executing activities related to NPD / NPT within the timeline defined by Project dept.
• Quality Orientation: Ability to understand process requirements, define quality standards, resolve problems relating to form fit functions.
• Stakeholder management: Capability to liaison and influence quality, production engineering and projects teams; work cross functionally in line with overall goals
• Talent management: Managing experienced professionals, assuring succession & workforce planning, resource allocation & organizational capability
Competencies
Values: Integrity, Accountability, Inclusion, Innovation, Teamwork
Compensation
• Competitive base salary commensurate with experience: $xxx – xxx (subject to change dependent on physical location)
• Posted salary ranges are made in good faith. TE Connectivity reserves the right to adjust ranges depending on the experience/qualification of the selected candidate as well as internal and external equity.
What TE Connectivity Internship Program offers
TE has a robust internship program that provides our interns with an abundance of resources to feel included as part of our Team. Every summer we coordinate various educational and networking events for our interns. The TE University Relations team will be hosting virtual meetups, information sessions, tours, skill building presentations, and topping it off with National Intern Day celebration activities.
A unique employee resource group we have is the Young Professionals Employee Resource Group (ERG). This group is committed to creating a highly engaged and empowered cross-functional network of young professionals by placing high value in Professional Development, Networking Opportunities and Community Involvement to drive the success of our interns.
In addition to the ERG, we also provide our interns with complete access to our internal library of self-lead courses. These courses include academies like leadership to help the interns develop their development in becoming future leaders at our organization. To help with their professional growth, we provide access to Mentors via our NAVIGATE platform. Mentors serve as a guide to navigate the organization and provide additional support in their career endeavors at the company. Our program provides a holistic experience for interns that targets professional development and personal growth.
Our internship program typically runs May thru August and gives students the opportunity to work on projects that contribute to the success of their team and build on their classroom experience. Throughout the 10–12-week program, interns will be provided with:
• Onboarding & Orientation
• Professional Development Workshops
• Networking Opportunities
• Operations Experience
• Executive Exposure
Timeline
TE Connectivity recruits on campus between September and March for New Grad (FT), Rotational, Internship and Co-op positions beginning in May. Once you have applied to a position, your resume and application will be reviewed. If you are selected to move to the next step in the application process, you will be contacted by a recruiter. Once you accept an offer, the onboarding process will begin in January for interns who have committed to offers in the fall semester and upon acceptance for interns who have committed to offers in the spring semester.
EOE, Including Disability/Vets
Location:
BANGALORE, KA, IN, 560 048
City: BANGALORE
State: KA
Country/Region: IN
Travel: Less than 10%
Requisition ID: 129451
Alternative Locations:
Function: Manufacturing
TE Connectivity and its subsidiaries, affiliates, and operating units (collectively, the "Company") is committed to providing a work environment that prohibits discrimination on the basis of age, color, disability, ethnicity, marital status, national origin, race, religion, gender, gender identity, sexual orientation, protected veteran status, disability or any other characteristics protected by applicable law or regulation.